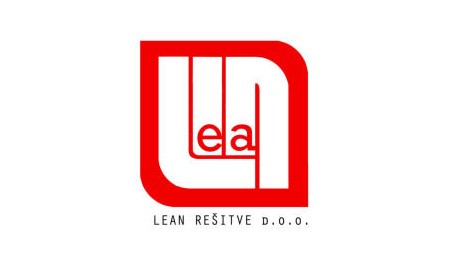
Galerija slik
Predstavitev
Smo skupina posameznikov z visoko stopnjo strokovnega znanja na področjih vitke proizvodnje, optimizacije proizvodnje, planiranja procesov pri širitvi podjetja in organizacije logistike. Ker vsi verjamemo in smo sami okusili pozitivne učinke vitke proizvodnje želimo skupaj z vami poiskati kreativne ideje in jih implementirati skupaj z vami.
LEAN KORAKI
Pot do uspešne vpeljave vitke proizvodnje se začne s 4 koraki.
Prvi Lean korak: PROBLEM
V vsakem podjetju se srečajo z različnimi izgubami:
• izgube zaradi prekomerne proizvodnje
• izgube zaradi čakanja
• izgube zaradi transporta
• izgube zaradi delovnega procesa
• izgube zaradi velikih zalog
• izgube zaradi premikov
• izgube zaradi proizvodnih napak
Prvi korak do REŠITVE je spoznanje da so določena prepričanja in dejanja napačna/neučinkovita.
Drugi Lean korak: ANALIZA
Za pravi uspeh je potrebna dobra analiza trenutnega stanja.
LEAN Rešitve se vsakega problema lotijo najprej s hitro analizo, z obiskom podjetja in ogledom proizvodnje.
Pridobljene informacije nam služijo pri pripravi ponudbe.
Tretji Lean korak: PONUDBA
Ker je vsaka proizvodnja zgodba za sebe so tudi ponudbe individualno prilagojene našim poslovnim partnerjem.
Ponudba oz. projekt je oblikovan okoli ključnega potenciala, ki je bil ugotovljen v fazi analize.
Četrti Lean korak: IMPLEMENTACIJA
Priprava LEAN organizacije, kreiranje terminskega plana in šolanje zaposlenih so samo 20% implementacije praktičnih LEAN rešitev.
Saj v proizvodnji skupaj z zaposlenimi in vodstvom 80% časa uvajamo LEAN.
METODE
LEAN
Glavni cilj vitke proizvodnje je odstraniti vse možne nepotrebne operacije, ki ne dodajajo dodane vrednosti končnemu izdelku in se jih lahko izognemo, hkrati pa zagotovimo, da delo poteka čim bolj enakomerno in stabilno.
Na razpolago imamo različna svetovno priznane metode, ki nam omogočajo, kako podjetje pripeljati do stopnje, da za izdelavo istega produkta potrebujejo.
manj časa,
manj delovnih sredstev
in manj vezanega kapitala.
TPM
TPM (“Total Productive Maintenance”) je koncept popolnega produktivnega vzdrževanja za nenehno izboljševanje skupne učinkovitosti strojev ob aktivni udeležbi vseh delavcev. Cilj preventivnega vzdrževanja je odpravljanje izgub: izgub zaradi izpada naprav, izgub zaradi menjave orodij in nastavitev izgub, zaradi praznega teka in zastojev, izgub zaradi zmanjšane hitrosti takta, izgub zaradi težav ob zagonu, izgub zaradi kakovosti.
6S
Koncept 6S predstavlja preprosto, toda učinkovito metodo organizacije delovnega mesta in služi za zagotavljanje čistoče in reda na delovnem mestu.
Pri doslednemu uresničevanju lahko poleg izboljšanja delovnih pogojev, timskega dela, razpoložljivosti orodij ali zadovoljstva kupcev zniža čas iskanja materiala, stroške skladiščenja in čas pretoka materiala.
KAIZEN
Izraz “Kaizen” izvira iz japonščine in pomeni nenehno izboljševanje vseh procesov v podjetju; lahko ga primerjamo tudi s stremenjem k popolnosti.
Temeljnega pomena je misel, da ni nič, tako kot je, že dobro. Če to prenesemo na situacijo v podjetju, pomeni, da ne obstaja ne obrat, ne izdelek, ne proizvodnji tok in ne proces, ki ne bi dopuščal možnosti izboljšave.
SMED
Koncept enominutne menjave orodij (“Single Minute Exchange of Die” - SMED) predstavlja metodo zmanjšanja neproduktivnega časa pri menjavi orodij, ki ne ustvarja vrednosti.
S pomočjo preprostih mehanizmov s tem omogoča bolj prilagodljivo proizvodnjo, ki proizvaja glede na potrebe (model mešane proizvodnje).
VSM
Filozofija vitke proizvodnje postavlja v ospredje obravnavanje pojma “vrednost” oziroma obratovalne procese ustvarjanja vrednosti.
Tako se pri vsakršnem začetku izboljšav stoji v središču pozornosti odpravljanje razsipnostih vseh možnih oblik – torej v vseh procesih, ki ne ustvarjajo vrednosti.
KANBAN
Da zagotovimo, da imamo na razpolago določen kos v določeni količini na določenem mestu ob določenem času, (“Just In Time”), uporabimo sistem “Kanban”, ki zagotavlja nenehno izmenjavo informacij v proizvodnji.
Proizvodnja morajo potekati v enem toku. Velikost lota mora biti nizka. Nihanja v povpraševanju se morajo predvideti z izenačevanjem in izravnavanjem proizvodnje.
LEAN KORAKI
Pot do uspešne vpeljave vitke proizvodnje se začne s 4 koraki.
Prvi Lean korak: PROBLEM
V vsakem podjetju se srečajo z različnimi izgubami:
• izgube zaradi prekomerne proizvodnje
• izgube zaradi čakanja
• izgube zaradi transporta
• izgube zaradi delovnega procesa
• izgube zaradi velikih zalog
• izgube zaradi premikov
• izgube zaradi proizvodnih napak
Prvi korak do REŠITVE je spoznanje da so določena prepričanja in dejanja napačna/neučinkovita.
Drugi Lean korak: ANALIZA
Za pravi uspeh je potrebna dobra analiza trenutnega stanja.
LEAN Rešitve se vsakega problema lotijo najprej s hitro analizo, z obiskom podjetja in ogledom proizvodnje.
Pridobljene informacije nam služijo pri pripravi ponudbe.
Tretji Lean korak: PONUDBA
Ker je vsaka proizvodnja zgodba za sebe so tudi ponudbe individualno prilagojene našim poslovnim partnerjem.
Ponudba oz. projekt je oblikovan okoli ključnega potenciala, ki je bil ugotovljen v fazi analize.
Četrti Lean korak: IMPLEMENTACIJA
Priprava LEAN organizacije, kreiranje terminskega plana in šolanje zaposlenih so samo 20% implementacije praktičnih LEAN rešitev.
Saj v proizvodnji skupaj z zaposlenimi in vodstvom 80% časa uvajamo LEAN.
METODE
LEAN
Glavni cilj vitke proizvodnje je odstraniti vse možne nepotrebne operacije, ki ne dodajajo dodane vrednosti končnemu izdelku in se jih lahko izognemo, hkrati pa zagotovimo, da delo poteka čim bolj enakomerno in stabilno.
Na razpolago imamo različna svetovno priznane metode, ki nam omogočajo, kako podjetje pripeljati do stopnje, da za izdelavo istega produkta potrebujejo.
manj časa,
manj delovnih sredstev
in manj vezanega kapitala.
TPM
TPM (“Total Productive Maintenance”) je koncept popolnega produktivnega vzdrževanja za nenehno izboljševanje skupne učinkovitosti strojev ob aktivni udeležbi vseh delavcev. Cilj preventivnega vzdrževanja je odpravljanje izgub: izgub zaradi izpada naprav, izgub zaradi menjave orodij in nastavitev izgub, zaradi praznega teka in zastojev, izgub zaradi zmanjšane hitrosti takta, izgub zaradi težav ob zagonu, izgub zaradi kakovosti.
6S
Koncept 6S predstavlja preprosto, toda učinkovito metodo organizacije delovnega mesta in služi za zagotavljanje čistoče in reda na delovnem mestu.
Pri doslednemu uresničevanju lahko poleg izboljšanja delovnih pogojev, timskega dela, razpoložljivosti orodij ali zadovoljstva kupcev zniža čas iskanja materiala, stroške skladiščenja in čas pretoka materiala.
KAIZEN
Izraz “Kaizen” izvira iz japonščine in pomeni nenehno izboljševanje vseh procesov v podjetju; lahko ga primerjamo tudi s stremenjem k popolnosti.
Temeljnega pomena je misel, da ni nič, tako kot je, že dobro. Če to prenesemo na situacijo v podjetju, pomeni, da ne obstaja ne obrat, ne izdelek, ne proizvodnji tok in ne proces, ki ne bi dopuščal možnosti izboljšave.
SMED
Koncept enominutne menjave orodij (“Single Minute Exchange of Die” - SMED) predstavlja metodo zmanjšanja neproduktivnega časa pri menjavi orodij, ki ne ustvarja vrednosti.
S pomočjo preprostih mehanizmov s tem omogoča bolj prilagodljivo proizvodnjo, ki proizvaja glede na potrebe (model mešane proizvodnje).
VSM
Filozofija vitke proizvodnje postavlja v ospredje obravnavanje pojma “vrednost” oziroma obratovalne procese ustvarjanja vrednosti.
Tako se pri vsakršnem začetku izboljšav stoji v središču pozornosti odpravljanje razsipnostih vseh možnih oblik – torej v vseh procesih, ki ne ustvarjajo vrednosti.
KANBAN
Da zagotovimo, da imamo na razpolago določen kos v določeni količini na določenem mestu ob določenem času, (“Just In Time”), uporabimo sistem “Kanban”, ki zagotavlja nenehno izmenjavo informacij v proizvodnji.
Proizvodnja morajo potekati v enem toku. Velikost lota mora biti nizka. Nihanja v povpraševanju se morajo predvideti z izenačevanjem in izravnavanjem proizvodnje.
Zemljevid
Poslovna ocena
1 Mnenje
5.0 povprečje glede na 1 Mnenja
5 zvezdic
1
4 zvezdice
0
3 zvezdice
0
2 zvezdice
0
1 zvezdico
0
-
UčinkovitoStoritevKakovostOsebjeVečino usposabljanj na delovnih mestih.
Hitri kontakt
Šešče pri Preboldu 6C , Prebold, Savinjska
Dodatna kontaktna okna
Poslovna oblika:
LEAN REŠITVE, svetovanje in storitve, d.o.o.
Davčna št.:
98467603
Govorimo:
SI
Mobitel:
+386 (0)41 554 307
Mobitel:
+386 (0)31 725 011
E-mail:
info@lean-resitve.com
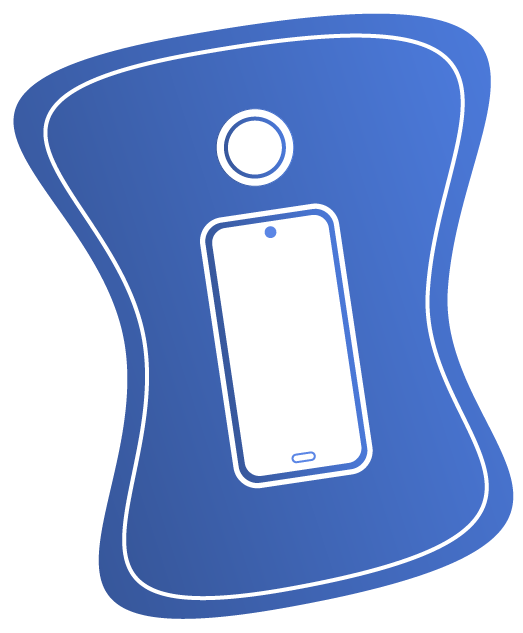
Certifikat - 2024

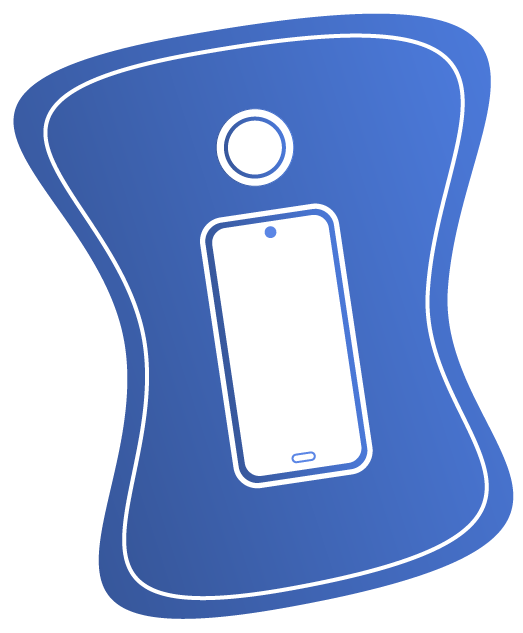
Certifikat - 2025

LEAN REŠITVE, PREBOLD